Push-Pull system removes welding fumes effectively
Welding fumes, grinding dust, oil mist: the metal industry produces all sorts of contamination. Welders and personnel in working areas are exposed to these air contaminants. It is essential to create healthy and safe working conditions by reducing these risks to health. Protective measures are an important aspect of this. So important, in fact, that strict international standards have been established to regulate them.
The challenge
ABB is well-known as a supplier of motors and generators and operates worldwide. ABB has many offices and production facilities that ensure the smooth operation of the high-quality products and systems.
This case study is about the production facility in Jüri, Estonia.
ABB Estonia was in the middle of a restructuring programme when the production lines were reviewed. As a result, one new welding working area was created. ABB contacted the authorised distributor of Plymovent in Estonia, MECRO, to find a suitable solution for the removal of welding fume.
All aspects were looked at on site, to ensure an optimal solution for this specific working area.
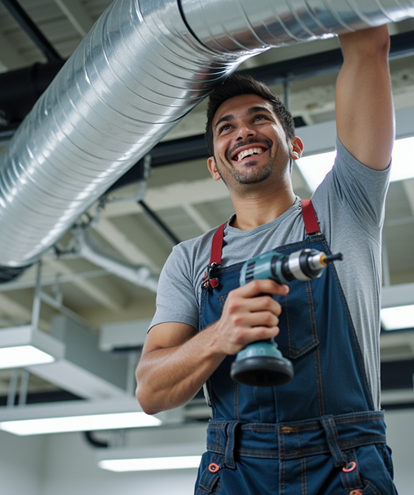
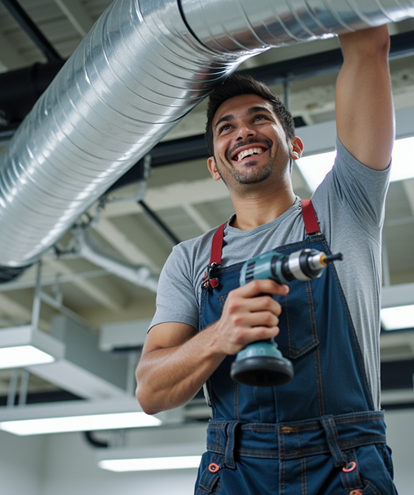
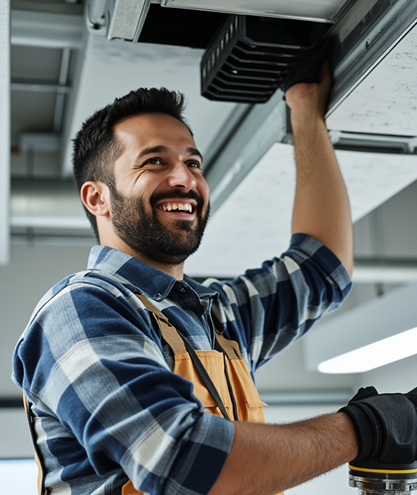
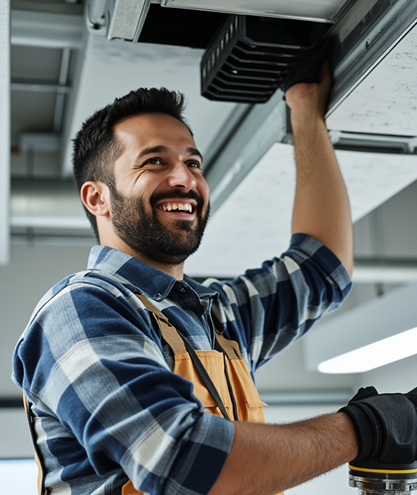
The solution
We have made it our business to control welding fumes with source extraction, hoods or general ventilation and filtration systems.
As ABB in Estonia was looking for a flexible welding fume extraction system, Plymovent opted for the Push-Pull system. This general ventilation and filtration system controls the concentration level of welding fume and ensures that the legal limits are not exceeded.
The working area where the Push-Pull system needed to be installed is 8 x 16 m. This working area is located in a production facility (hall) of 25 x 50 m.
Plymovent analised the situation and concluded the following:
- As the employees of ABB work with large metal workpieces, source extraction was no option.
- As the welding area is big (128 m2), an extraction hood is also no option.
The Push-Pull system is perfect for working areas like this. To make optimal use of the floor space, the filtration unit, fan and system control panel were placed on a construction platform. ABB went along with our recommendations to install the Constant Flow variant. A pressure transmitter installed in the ductwork is used to set the system volume at time of commissioning of the system. Logically, less power is required at time the filters are new. Depending on the operating hours, the pressuredrop of the system will slowly increase during the lifetime of the filters. This pressure increase will be sensed by the pressure transmitter, which on his turn will command the frequency controller, to adapt the rpm of the fan motor.
With this system a Constant Flow is achieved against the lowest possible energy use.
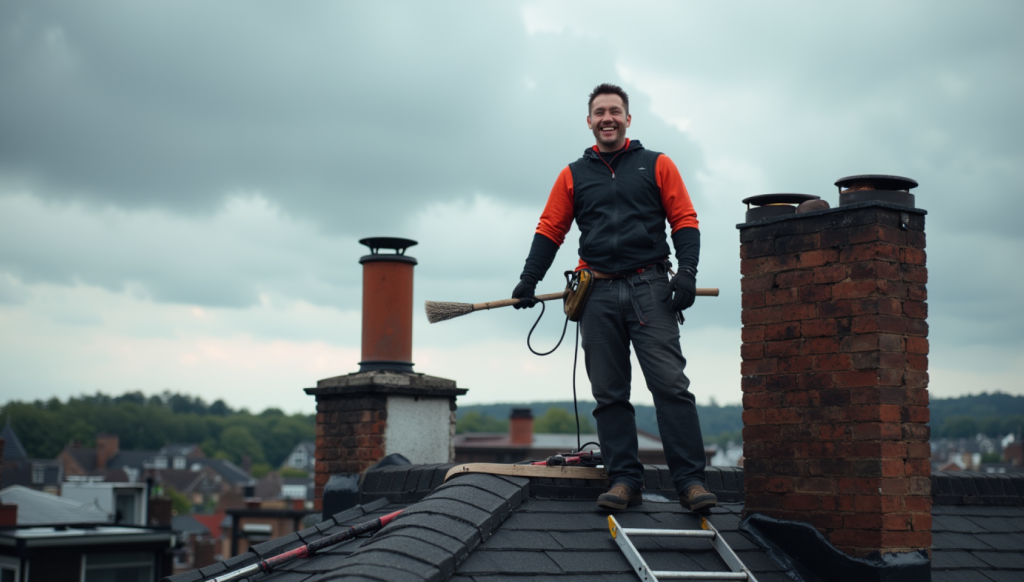
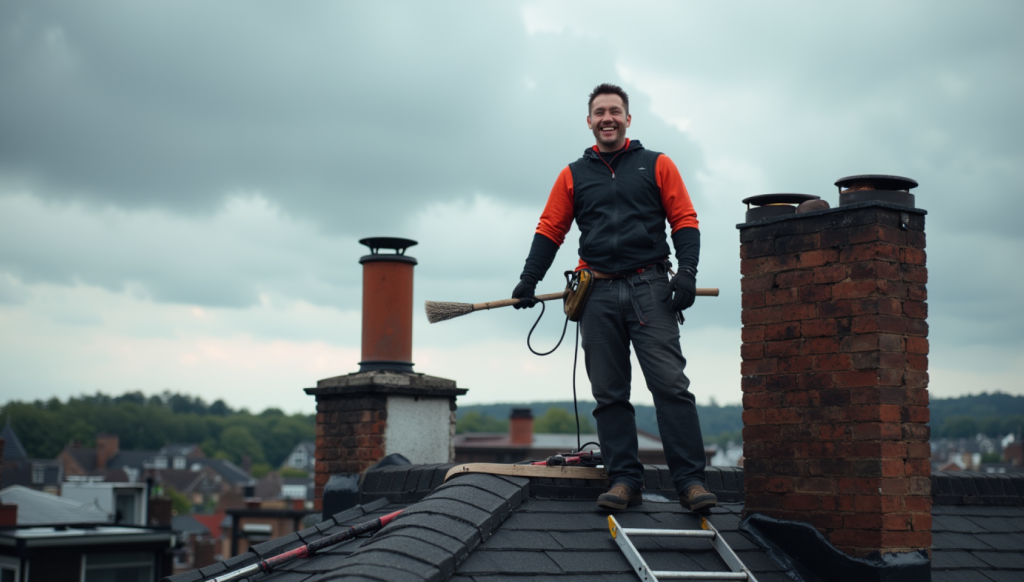
Main benefits
- A clean safe working environment right from day 1
- A clean building that will stay clean
- A new state of the art facility to be proud of which speaks volumes to their staff, their existing clients and their prospective clients alike
- Technology that supports the high profile required to operate as a respected global company
- A tool that supports attraction and retention of employees and adds value to prospective partners and clients